Digital Twin – Smart Flow
Description
Analysis of product flow improvements in industrial processes through the creation of virtual simulation models (digital twins). By analyzing manufacturing processes via digital replicas, it is possible to accurately and proactively assess the impact of new plans or changes, providing a shared understanding of future workflows across the company.
This service enables a variety of analyses, including:
- Evaluation of new layouts using process simulation techniques
- Model integration with company data sources
- Sensitivity analysis of parameters
- Process cost optimization analysis
Competitive Advantages
- Development of “discrete event simulation”, “multi-agent simulation”, and “mixed simulation” models. Capability to integrate simulation models with real-time process information systems.
- These services help companies redesign layouts, reduce costs, optimize resource usage, analyze bottlenecks, and assess investments or layout changes before implementation.
- They also support the virtual assessment of new facilities, such as evaluating the integration of new automation technologies into processes (e.g., replacing conventional systems with AGVs).
Applications
- Optimization of internal material movement processes to assess resource utilization within the company
- Performance analysis of a new plant or warehouse before its physical setup, to determine the required infrastructure
- Automated design and evaluation of new plant or warehouse layouts
- Internal logistics analysis for companies considering AGV implementation, allowing validation and dimensioning of their deployment
- Identification and analysis of bottlenecks and saturated areas
Keywords
Digital twin, process simulation, layout, AGV, automation, virtual model, multi-agent simulation, discrete event simulation
Contact
Success Stories
LINDE-WIEMANN
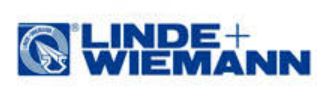
Definition and validation of the optimal movement solution using a digital twin (best AGV usage-to-number ratio via LEAN design while maintaining machine availability) for integrating an automated internal logistics system.
Value delivered to the company (Juan Carlos Dueñas, Plant Manager):
"The collaboration with ITAINNOVA to implement these new internal logistics processes has been extremely helpful. From the beginning, the simulation of our material flows allowed us to identify the critical areas we would face once the real process was implemented. It also enabled us to run simulations of potential new scenarios, which supported our final decision-making process..."
SCHMITZ CARGOBULL
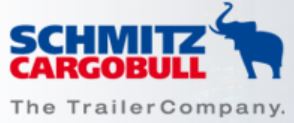
Design and analysis of the configuration, production resources, and intralogistics of the new SCHMITZ CARGOBULL industrial plant using a digital twin, based on the creation of a dynamic digital twin.
SKF
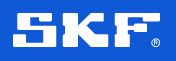
Digital twin of internal material handling processes—carried out by forklift operators and AGV systems—developed using real operational data provided by SKF Española. The goal was to evaluate resource usage within the manufacturing plant and improve internal logistics processes.
PSA Groupe
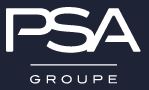
Design and development of a chaotic buffer management system using AGVs.